New assembly video with focus on important details
Date:
Author: Rune Jungberg Pedersen, Communications & CSR Director
Category: Attractive Stores , Compliance and Quality
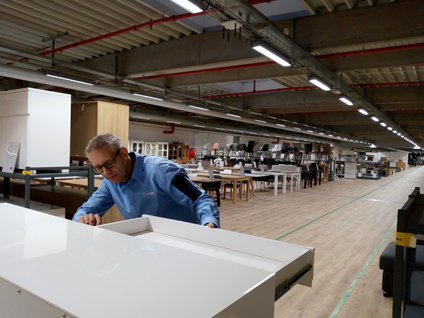
To ensure that customers always get a great experience in JYSK, it is crucial that all display furniture is assembled in the right way.
Sideboards which are lower in the middle, drawers which are not adjusted or lacking handles are just some examples of how badly assembled furniture will result in a bad customer experience.
Therefore it is crucial that display models in the stores are correctly assembled and adjusted. Just as this is the case in the home of the customers, if they are to be fully satisfied with the self-assembly furniture.
“We work in a number of ways to make it easier to assemble and adjust furniture from JYSK," explains Quality Assurance Specialist Torben Ladefoged Gjørret.
“First of all the construction of the furniture needs to be right. Is must be easy to assemble, and the number of different brackets should be as small as possible. Furthermore the assembly manual must be easy to read and understand," says Torben and adds:
“Regarding assembly manuals we have made a lot of changes. For example we have designed our own templates and drawings of tools, so the manuals besides being informative and understandable also have a nice and uniform expression. This is something we have received a lot of positive feedback on."
To make assembly easier Compliance & Quality has produced a new video with guidance on how to ensure that furniture are assembled and adjusted in the right way.
Assembles everything
Torben Ladefoged Gjørret
- 1988-1991 Woodworker Apprentice (QuistFurn A/S)
- 1991-2002 Product Developer and then Production Manager (QuistFurn A/S)
- 2002-2004 Product and Production Supporter (Velfac A/S)
- 2004-2017 Product Development Manager (Interstil)
- Since January 2018 – Quality Assurance Specialist at JYSK
Another important element is that Torben or one of his colleagues in the Quality department have a thorough look at all new pieces of furniture, before they are accepted as part of the JYSK assortment. During that process they also ensure that the furniture are constructed in the right way, and that they live up to JYSK's requirements regarding product quality.
“Assembly is part of that process. That is the only way to ensure that all steps in the assembly manual are correct and easy to understand,” says Torben.
“As soon as the first shipment of furniture arrives at our distribution centres, we do a quality control and test assembly, and nothing is sent to any of our stores, before this is done,” he says.
That, along with the video which he hopes all JYSK employees will find time to view, are some of the actions which are made to reduce the number of complaints and calls to Customer Service.
That the video is also available to the broad public through GOJYSK.com, is something that Torben is very happy about.
“The video contains advice which everyone can benefit from, and it is very much in the interest of JYSK to make it as easy as possible for our customers to assemble JYSK furniture. That is an advantage for both our customers and for JYSK,” he says.