The art of packing a pallet
It takes planning and experience to pack a pallet of goods that is easy and fast to handle in stores.
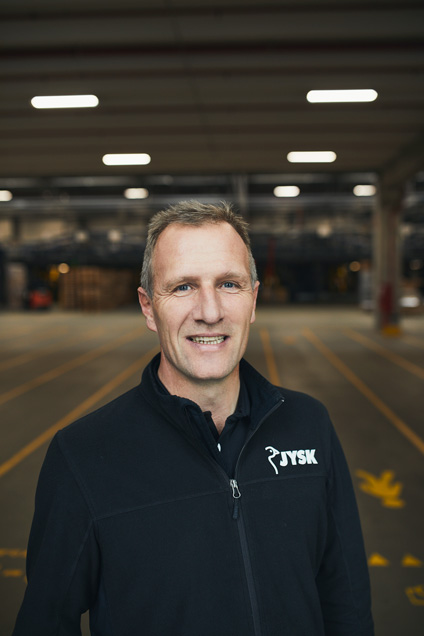
”How hard can it be to pack a pallet?”
Frede Jørgensen, Warehouse Manager at JYSK’s distribution centre in the Danish city of Uldum, understands why people would ask that question. Especially his store colleagues, who receive the pallets with goods from the distribution centre.
As employee number 24 in JYSK, by now Frede has enough experience to know that reality is more complex than that.
”You really have to tip your hat to the people who pack the pallets with goods. Every time, this is really a puzzle to solve, and it takes very high levels of precision. Sometimes mistakes happen, but we do our very best to avoid them,” says Frede, who on 1 November celebrated his 35-year anniversary in JYSK.
From distribution centre to store
Every package is weighed and measured all the way from its arrival at the distribution centre, until it is sent by truck to a JYSK store, in order to secure the optimal placement when it is packed on a pallet.
Some products that arrive in several packages are delivered ready to be sent directly to stores without leaving the pallet.
”If, for instance, a sofa consists of three packages, we ask the supplier to pack all three units on one pallet whenever possible. That way we can quickly and easily transport the pallet to and from the trucks and send it on to the stores, where it can then be stored on the pallet until the customer picks it up,” says Frede.
Many packages do travel to and from the distribution centre: the stock turnover ratio, which is the technical term, is actually so high that all products arriving at the distribution centre in principle leave again no later than three months later.
Employees learn from each other
One of the most experienced employees who packs pallets in Uldum is Jens Peter Mikkelsen. He has worked as a so-called picker for almost 15 years, and every day he solves the puzzle of packing products on pallets in the best possible way.
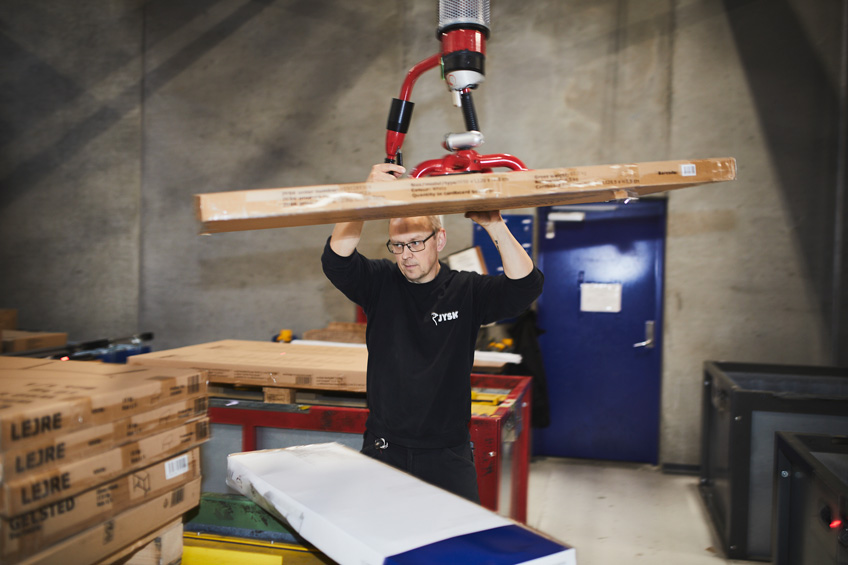
On a regular basis, Store Managers visit Jens Peter in Uldum to see how things work at the distribution centre. The visits are educational both for him and for his store colleagues.
Facts about TDR
- Via an internal system, TDR, stores can report issues with pallets, for instance with photos of the issue.
- The reports are sent to the distribution centre employees, who can then follow-up on the issue and send feedback to the store.
- TDR is short for Transport Delivery Report.
“Sometimes my colleagues from the stores wonder why some of our furniture is separated on different pallets instead of being delivered together. But when they see for themselves how we pack the products it becomes clear to them that packing the products together is not always an option,” says Jens Peter.
At the same time, the visits have made Jens Peter aware that his colleagues would like small boxes together on the same pallet. This makes it easier to collect them on a trolley and move them to the store warehouse.
See how goods are handled below:
First, products arrive by truck to the distribution centre.
Then the products are moved to one of the high-bay warehouses.
From the high-bay, the products are transported via a conveyor belt to the so-called picking stations.
At the picking stations, Jens Peter Mikkelsen and his colleagues pack the products on pallets.
Finally, the packed pallets are moved to the trucks that deliver them to stores. (Photos: Rune Slettemeås/Mark&Bjerre.)